Industrial supply chains and how to maintain them in the coronavirus age were the topics of this week’s virtual round table discussion, hosted by the University of West Florida.
Representatives from a number of Pensacola-area business joined the discussion on ZOOM. The moderator was Scott Keller, a Professor of Marketing and Logistics at UWF.
“It’s broader than just Pensacola but it certainly is focused in our region,” said Keller. “Just to discuss important topics, ideas and issues surrounding supply chain and logistics impacting our region during this pandemic.”
Some of the participants are UWF graduates, who are now work for various companies, and have connected with the schools in other areas over the past 15 years.
“All of you have connected to us in ways; you’ve been in the programs that are now managers; you’ve been managers that have given us tours and worked with our students on projects,” said Keller. “And we wanted to share some of this discussion with you.”
“We work closely with our partner, and with GE on maintaining the social distancing; then being able to supply masks for all the workers,” Josh Mattson, a manager at Landrum Human Resources at Pensacola’s General Electric plant.
The emphasis, he says, if employee safety through limited physical contact.
“We’ve extended the break rooms, being able to open up more space to keep that distance between everybody,” said Mattson. “And then kind of shuffling some work schedules around, so we don’t have multiple people leaving or getting too close during our incoming and outgoing shifts.”
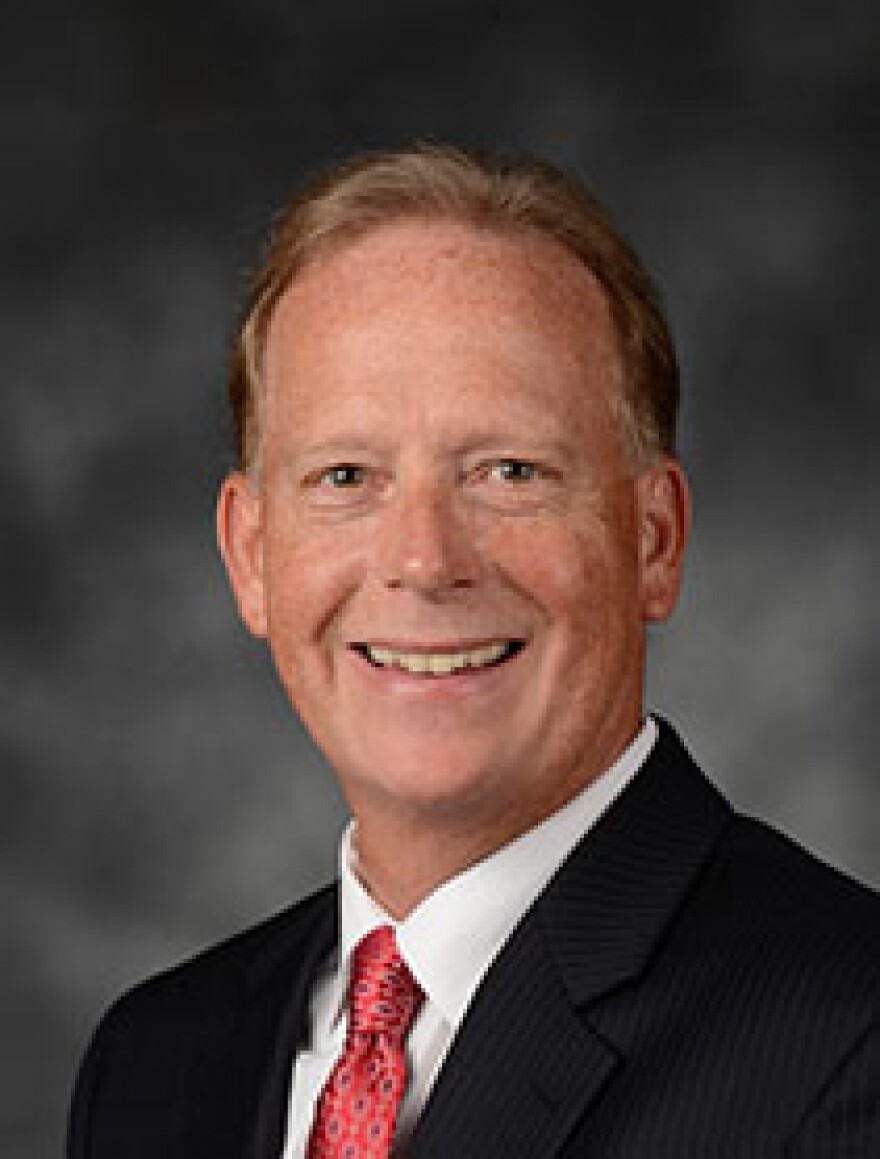
But not just the more than GE’s 500-plus employees. The firm is also working to protect vendors, visitors and others from exposure to the virus. That includes active screening – where one’s temperature is taken before entering the building – to using a thermal camera. If the supply operation is disrupted, it ripples through the industrial community. Mike Hallett at GE says it’s a matter of flexibility – being able to adapt.
“We meet on a daily basis and challenge ourselves – what can we do next? What haven’t we thought of? What can we do for tomorrow, and acting on that quickly?” Hallett said. “And also keeping the workforce in the know. We send out basically an ‘ad hoc communication’ that goes out to the entire workforce and lets them know here’s what’s going, here’s what to expect.”
Also online was John Stacey – Director of Supply Chair for Ascension Sacred Heart’s five hospitals from Mobile, Alabama to Port St. Joe. He says COVID-19 is producing a major challenge in balancing supply ability with operational needs and conservation.
“In a normal environment, it’s no big deal to put a mask on, use it for 5 min. and toss it in the trash,” Stacey said. “But in these types of environments, we’re looking at extending the life of those masks. [If] it’s not dirty after 5 min. let’s continue to use it.”
As long as the mask supply holds out, Stacey says the Ascension Sacred Heart chain can meet demand. But in this pandemic, situations – logistical and otherwise – can change literally hour-to-hour.
“Where we have to have discussions, is if we have to have more conservative approaches, what does that look like and how do we best implement it?” said Stacey. “And we don’t do that in a vacuum. Leadership can’t act without a supply chain, and a supply chain cannot act without leadership support. So it is definitely a team effort within the health care system.”
“Our primary industry is insurance restoration, so we respond after any type of water, fire, mold, vehicle impact, unattended deaths, storms, that type of events,” said Shawn Carpenter, whose firm Complete DKI, illustrates the interlocking nature of logistics and supply brought about by emergencies such as the coronavirus.
“One of the things that we’re doing a lot more of recently – we’ve done quite a bit with Ascension Sacred Heart, cleaning after confirmed COVID cases,” Carpenter told the session. “We’ve always done biohazard cleanup; basically the equipment and the tools we utilize for all of those, fall right in line with what’s needed for the COVID-19 cleanings.”
Three areas that companies should focus on post-coronavirus, according to PWC – an assurance, tax and consulting service -- include improving supply chain visibility; modeling new risks and costs, and concentrating on focus and resilience.